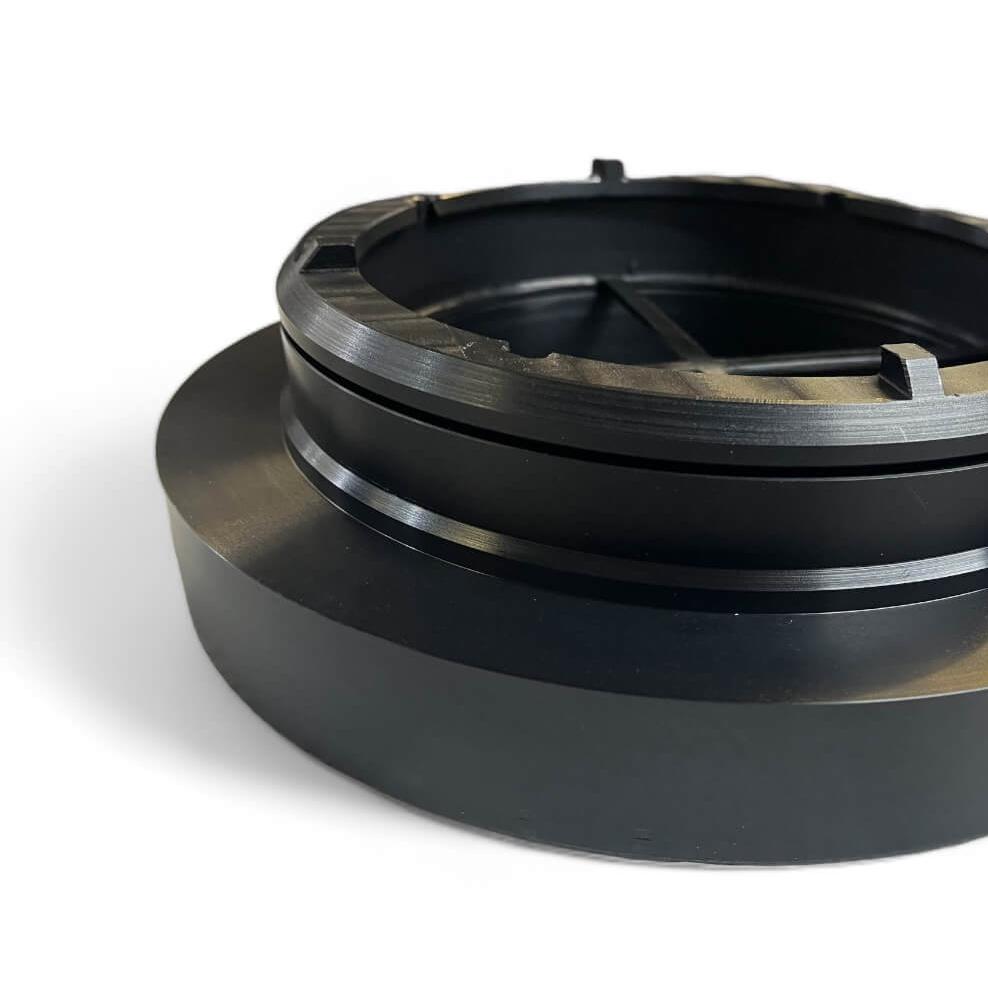
At WKH Group, we take pride in delivering high-quality, customised components for a diverse range of industries. Recently, we had the opportunity to design and manufacture seal-ring-carbon-PTFE parts for a customer in the subsea sector.
This project showcased our expertise in precision engineering and material science, particularly in the use of carbon-filled PTFE (Polytetrafluoroethylene) and our state-of-the-art CNC routing machines.
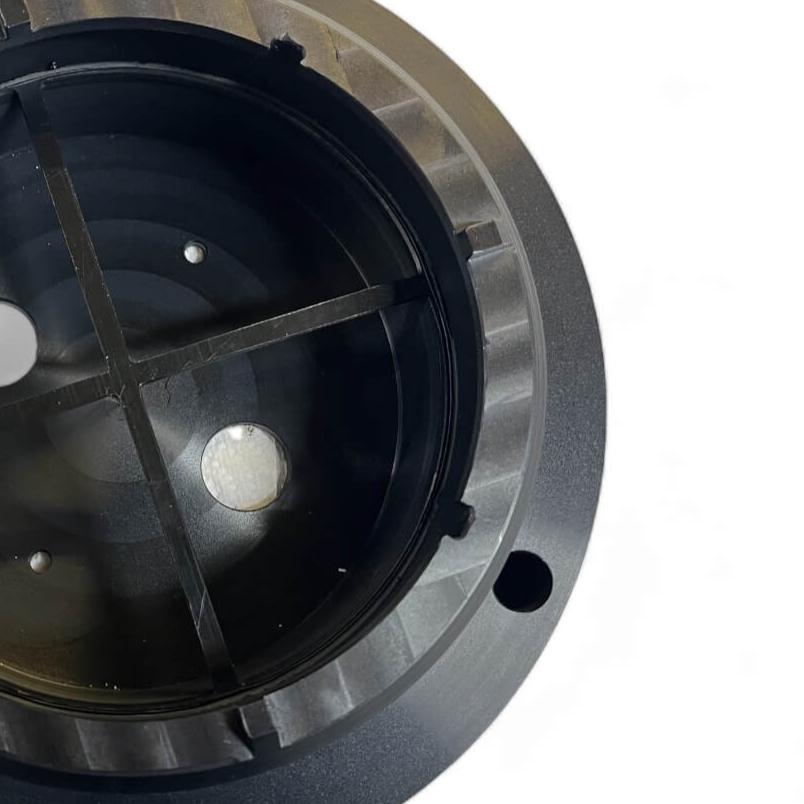
What our client required
The subsea sector demands materials that can withstand extreme underwater conditions, including high pressure, temperature variations, and corrosive elements. Our customer needed robust and reliable seal rings with superior sealing properties to prevent leaks and ensure equipment integrity. After assessing their needs, we recommended carbon-filled PTFE.
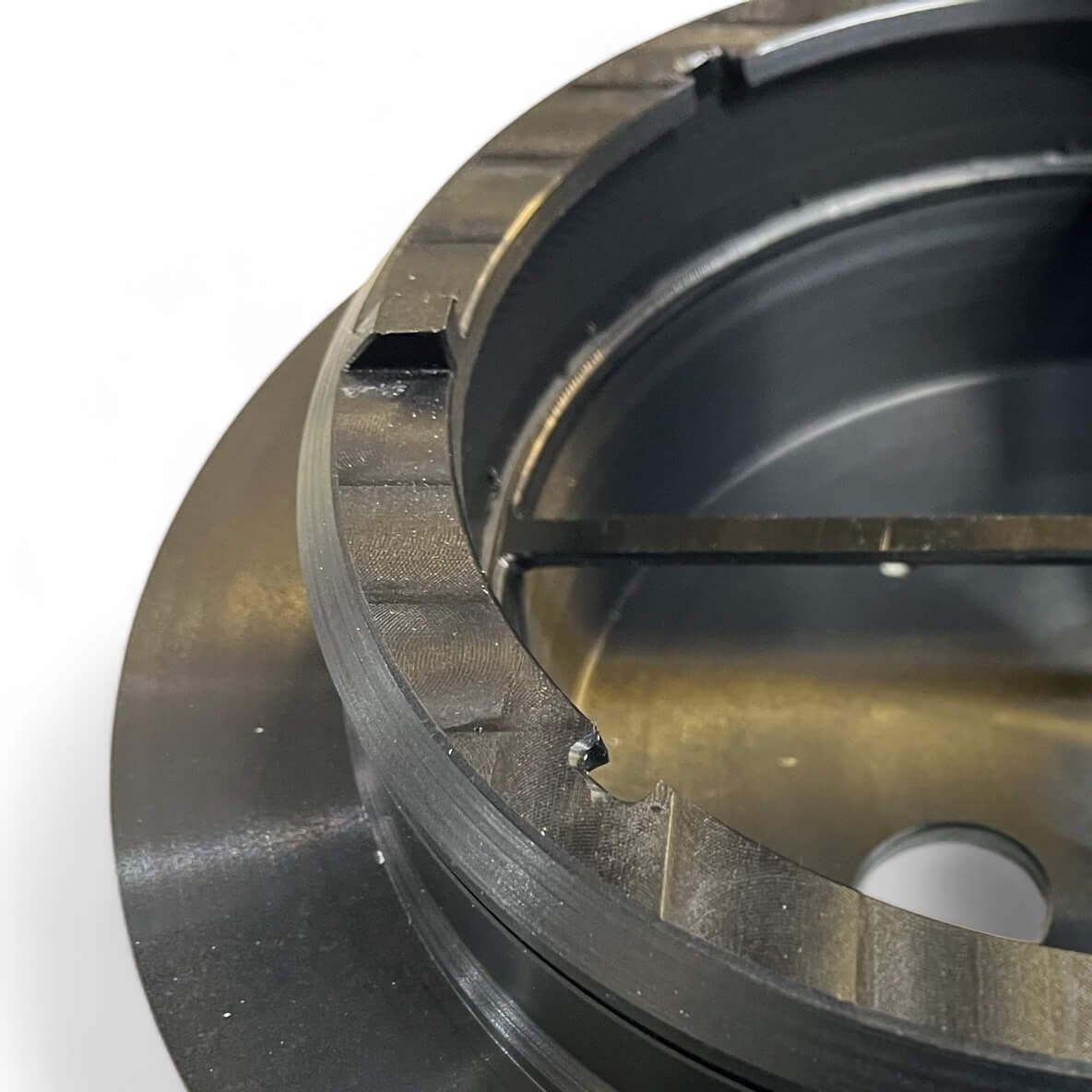
Why Carbon-Filled PTFE?
- Enhanced Mechanical Properties: Carbon fillers improve PTFE's compressive strength, wear resistance, and load-bearing capacity.
- Improved Thermal Conductivity: Better thermal management, crucial for subsea applications.
- Chemical Resistance: Maintains PTFE’s resistance to chemicals, oils, and corrosive substances.
- Dimensional Stability: Ensures the seal rings maintain their shape under high pressure.
- Low Friction and Wear Resistance: Results in longer-lasting seal rings with minimal maintenance.
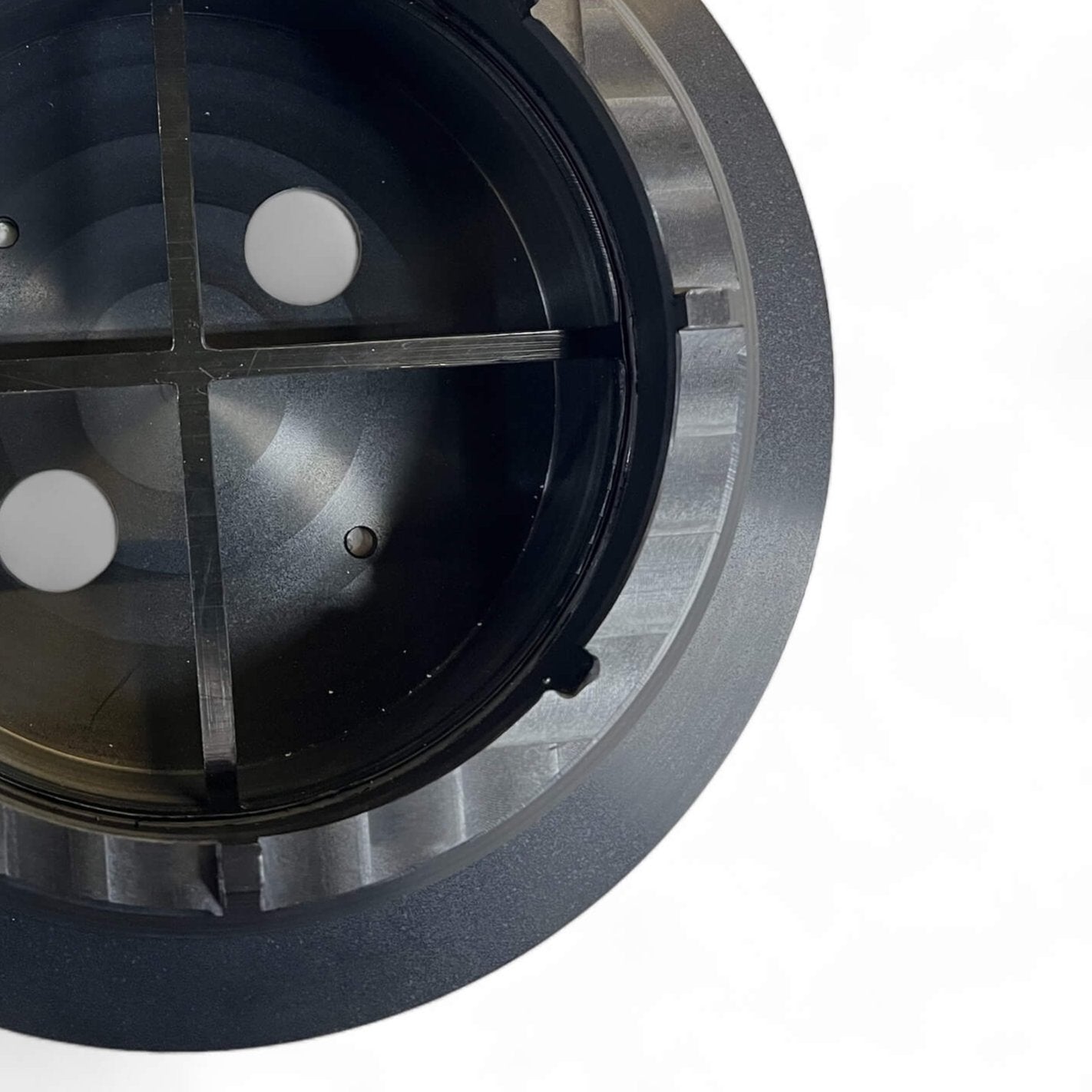
We utilised advanced CNC (Computer Numerical Control) routing machines for manufacturing. The process began with designing and prototyping using CAD software, followed by testing and validation. High-quality carbon-filled PTFE sheets were then prepared for machining.
The material was loaded onto CNC machines, which precisely shaped it into the desired seal ring geometry. Each seal ring underwent rigorous quality control, including dimensional inspection, surface finish evaluation, and performance testing. After passing these checks, the seal rings were deburred, polished, and prepared for shipment. CNC routing machines offer several advantages, including precision and accuracy for tight tolerances, consistency in producing identical high-standard parts, efficiency with faster production times, and flexibility to quickly reprogram for different parts or design adjustments.
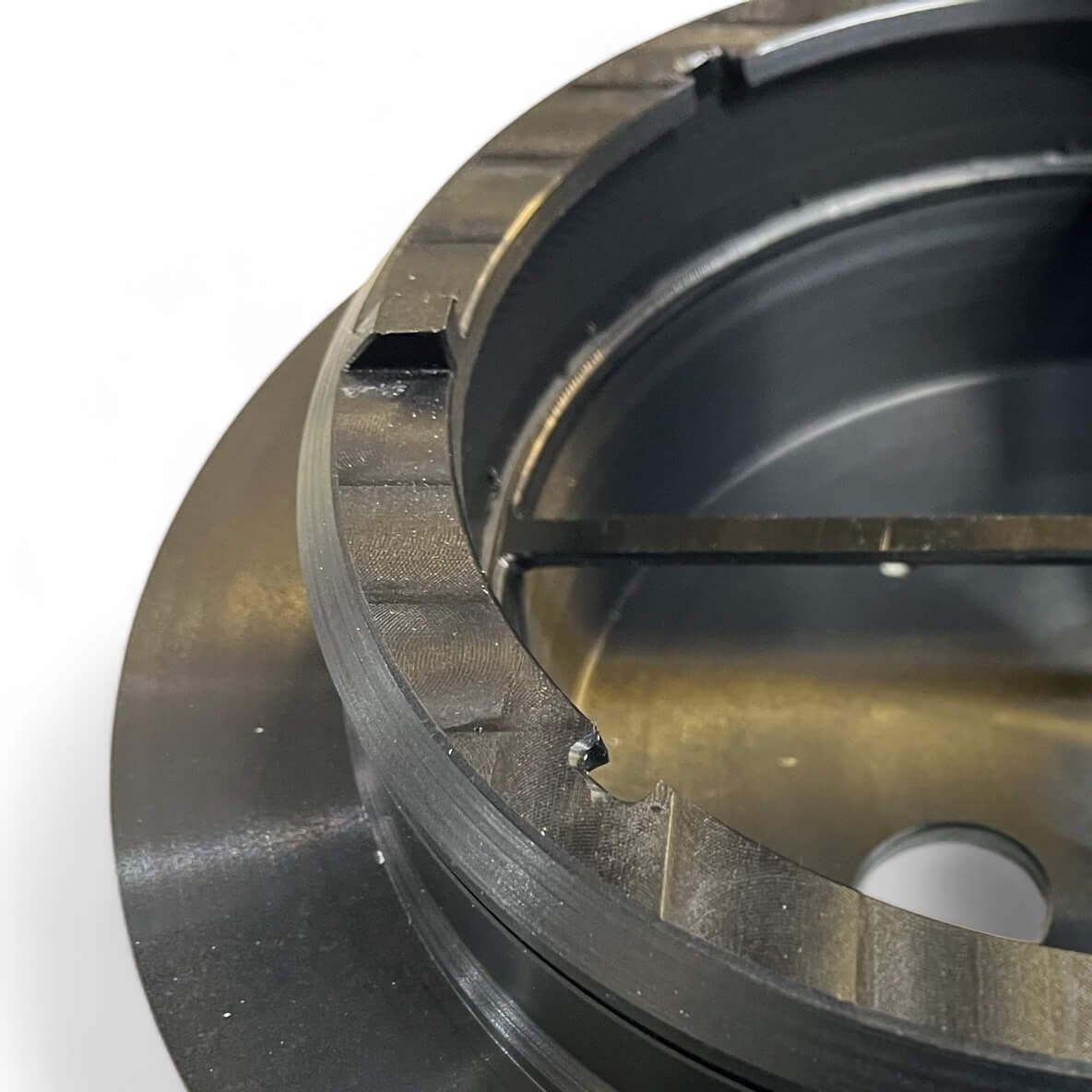
Final applications
At WKH Group, we are committed to excellence by using the best materials and technology. The seal-ring-carbon-PTFE parts for the subsea sector demonstrate our dedication to quality and innovation.
Leveraging the properties of carbon-filled PTFE and the precision of CNC routing, we delivered components that meet the rigorous demands of subsea applications. Our customised solutions, backed by engineering expertise and advanced manufacturing, ensure enhanced performance and reliability for our customers. We continuously invest in research, technology, and process improvements to remain a leading provider of high-performance components for challenging environments.
At WKH no project is too big, too small or too complex, for any precision engineering needs simply call us on 0113 239 1909, email us or request a quote.
Blog posts
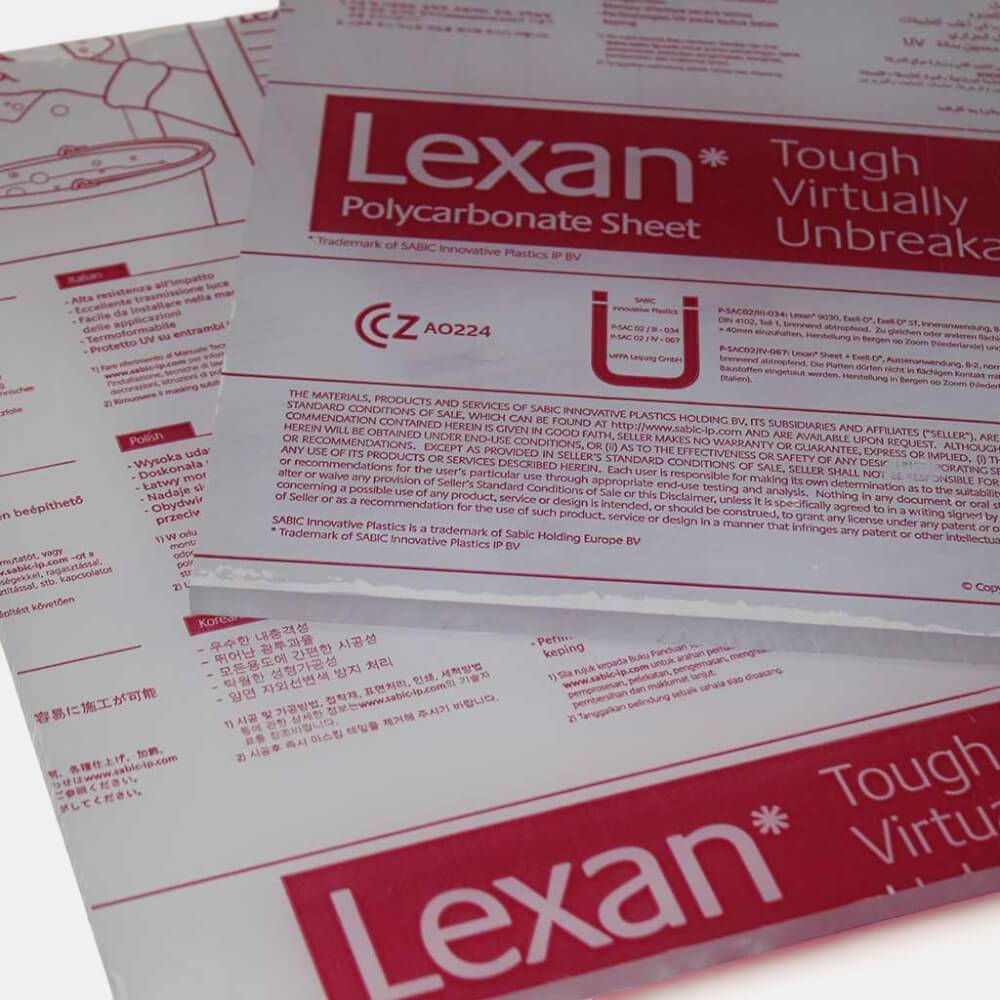
Lexan is a brand name for a type of polycarbonate resin thermoplastic developed by General Electric Plastics (now owned by SABIC). Known for its strength, durability, and optical clarity, Lexa...
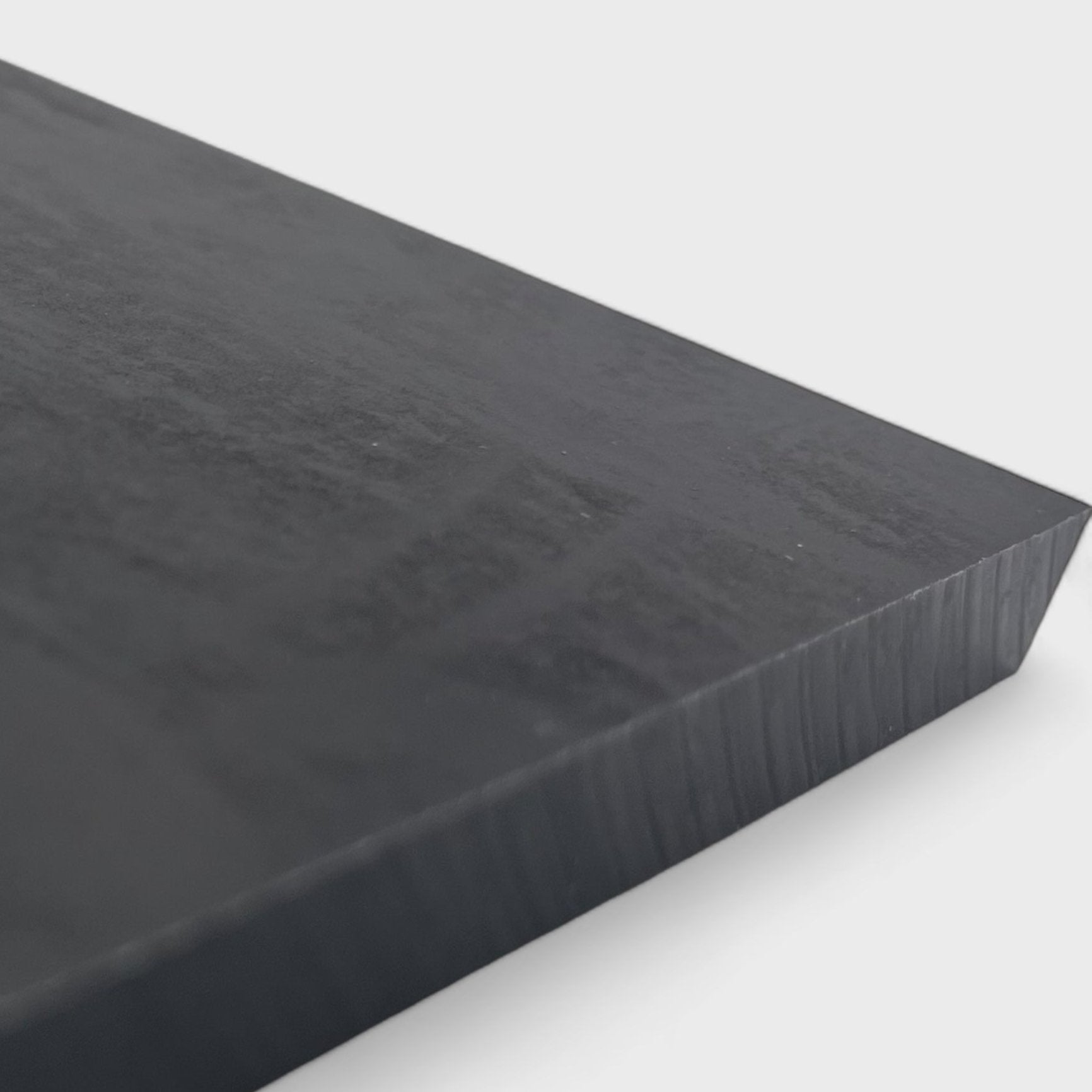
Teflon, a brand name commonly associated with the chemical compound polytetrafluoroethylene (PTFE), is a synthetic fluoropolymer of tetrafluoroethylene. First developed in the 1930s by Roy Plunket...

What is the density of High Density Polyethylene?
High-Density Polyethylene (HDPE) has a density range of 0.94 to 0.97 grams per cubic centimetre (g/cm³), which sets it apart from other types of polyethylene, such as Low-Density Polyethylene (LDP...