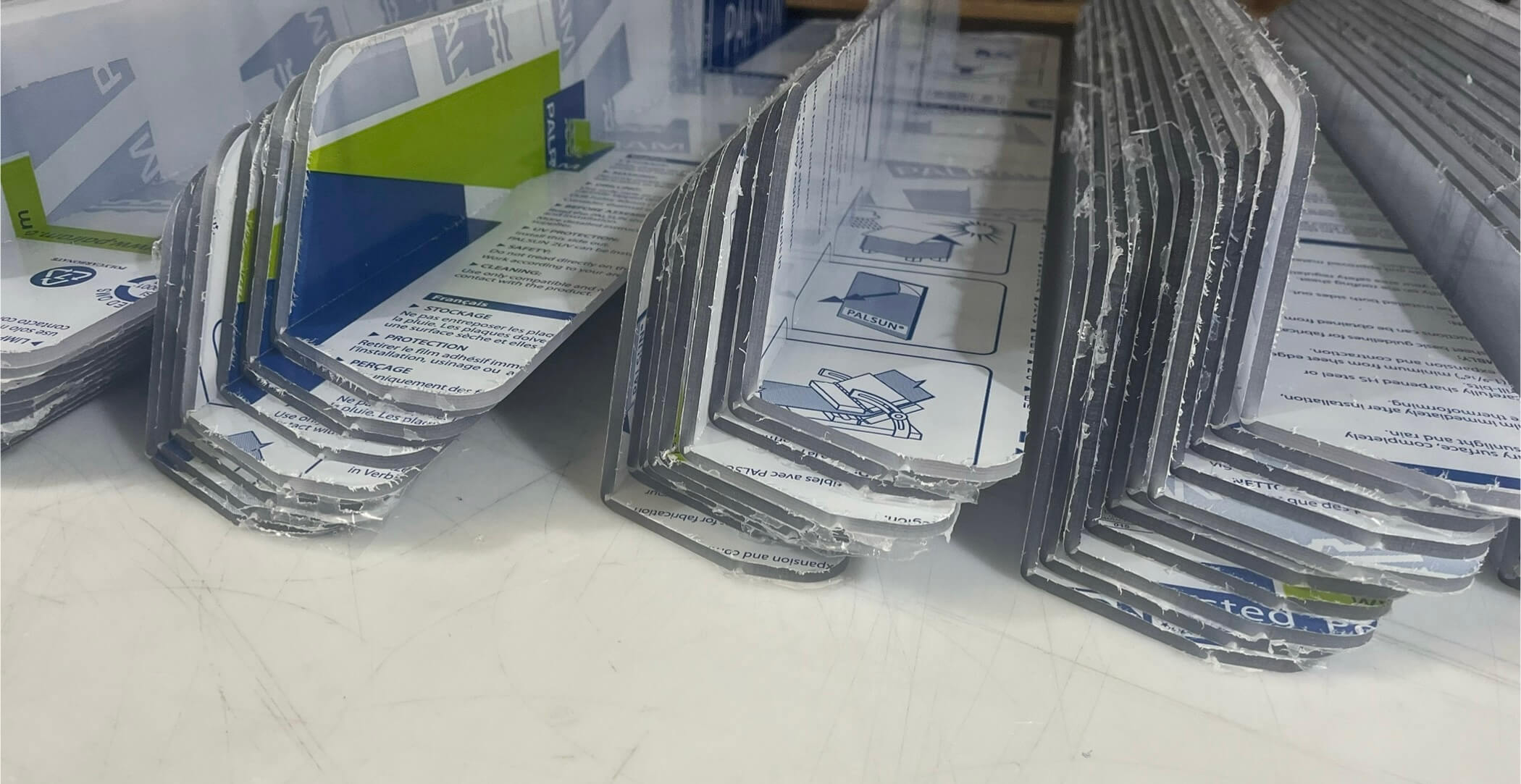
In the electrochemical sector, protection from hazardous materials and processes is essential. Polycarbonate shield screens are a popular solution due to their durability, clarity, and impact resistance, offering effective protection while allowing visibility.
This article covers the benefits, applications, and manufacturing process of polycarbonate shield screens, including precision bending and CNC routing to achieve a precise 90-degree angle.
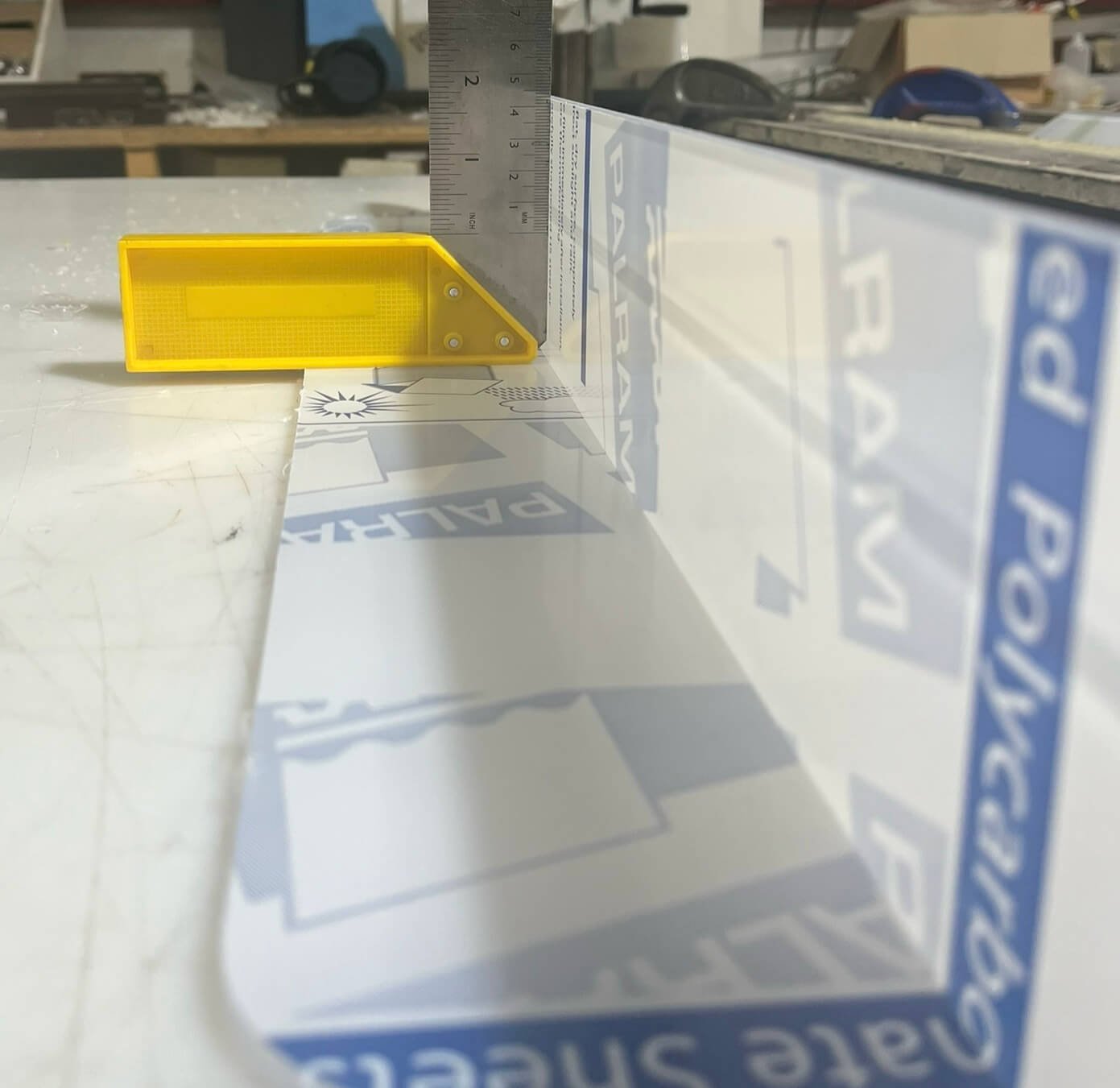
Key Features
- Impact Resistance: Polycarbonate screens are incredibly tough, capable of withstanding strong impacts without shattering. This durability is essential in environments where protection from flying particles or accidental impacts is necessary.
- Optical Clarity: These screens are transparent, offering clear visibility, which is crucial for monitoring electrochemical processes.
- Chemical Resistance: Polycarbonate offers resistance to many chemicals, making it ideal for environments where exposure to corrosive materials is likely.
- Thermal Stability: With high resistance to temperature fluctuations, polycarbonate screens are suitable for diverse industrial environments.
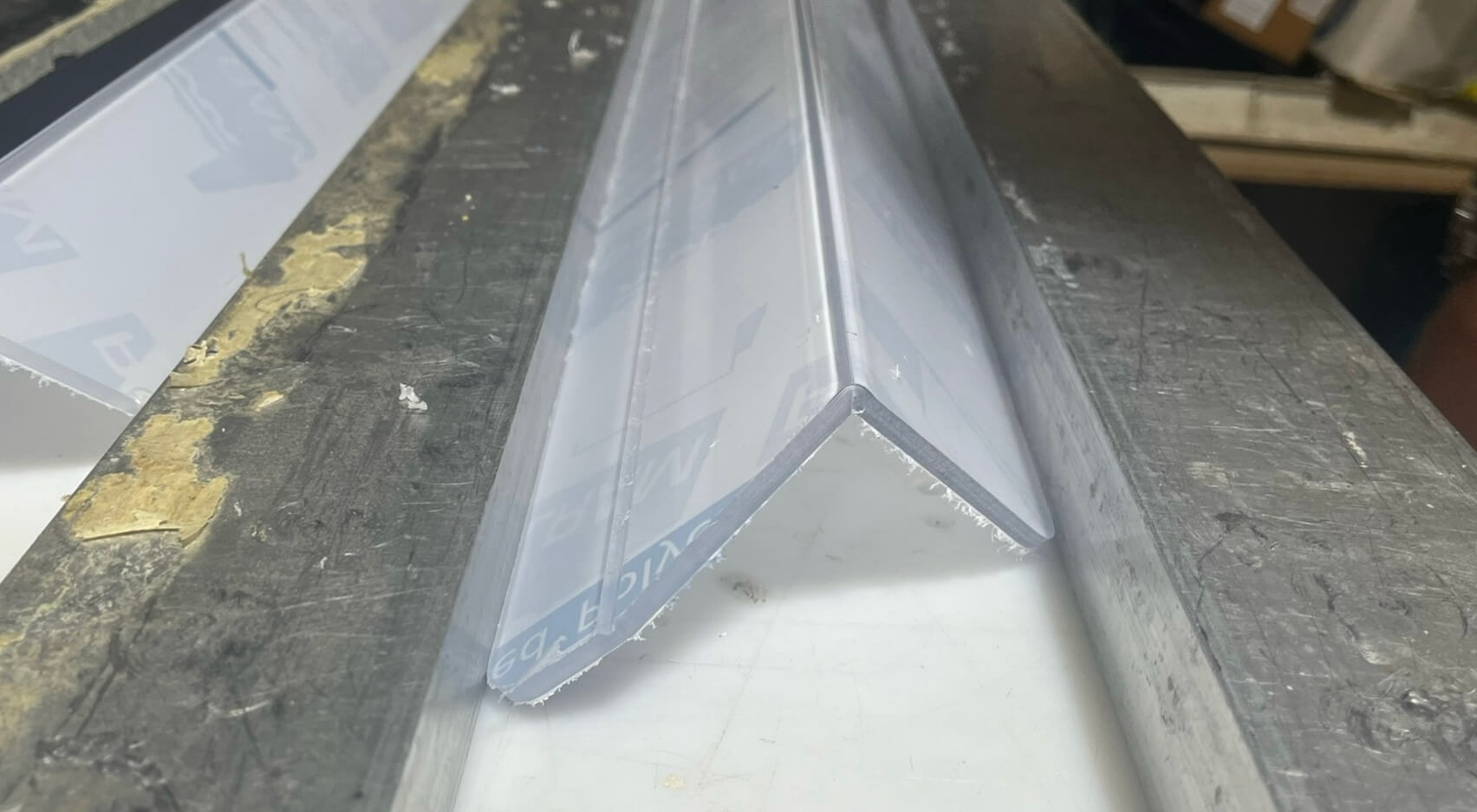
Applications in the Electrochemical Sector
In electrochemical operations, polycarbonate shield screens protect workers from splashes, chemicals, and debris produced during processing. These screens are used in various setups:
- Laboratory Enclosures: To protect laboratory technicians during experiments involving volatile materials.
- Production Facilities: For shielding automated machinery, reducing the risk of accidental exposure to chemicals and particles.
- Industrial Assembly Lines: To create a barrier between workers and potentially hazardous equipment, while maintaining visibility for supervision.
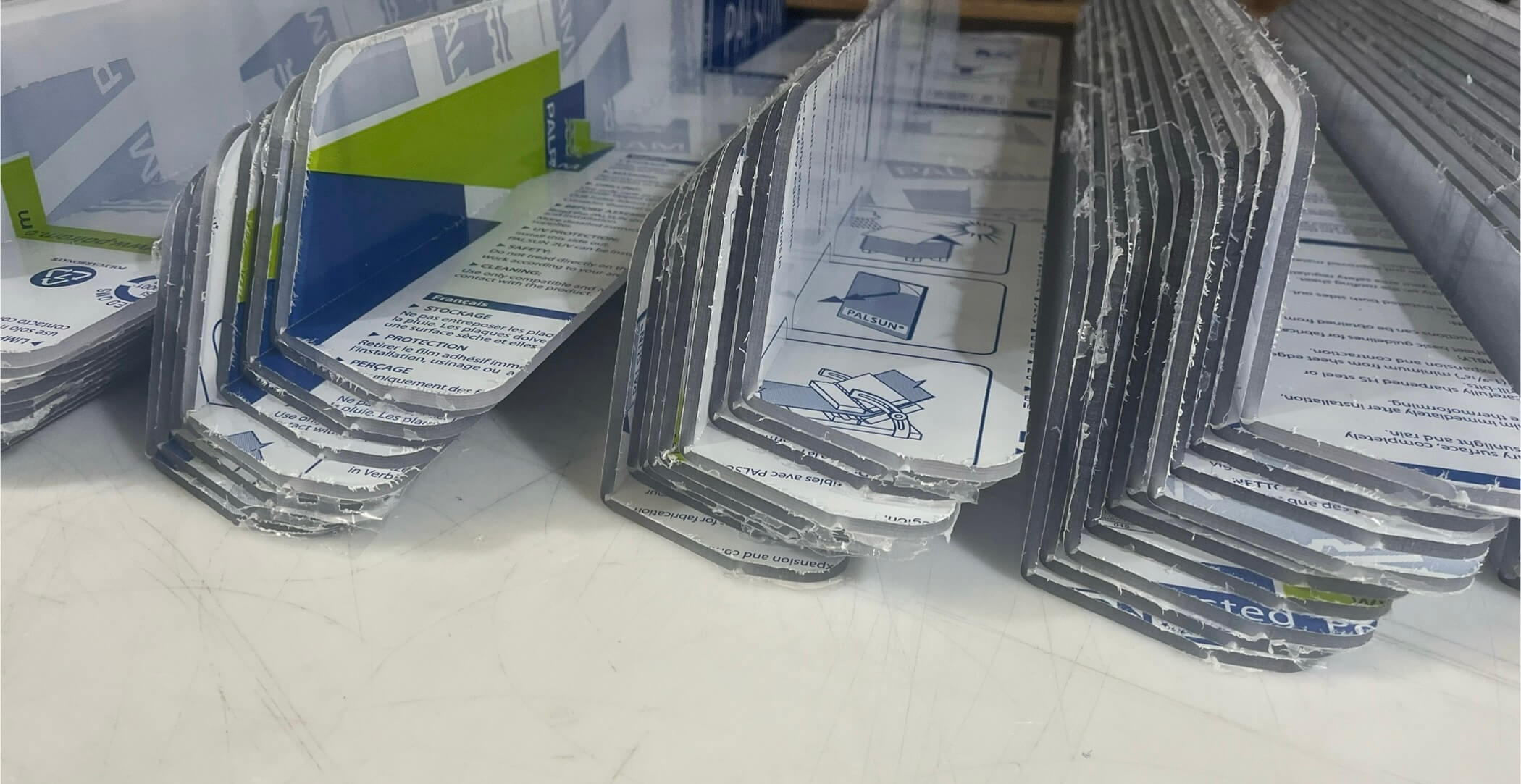
Manufacturing Process
Step 1. Material Selection: High-quality polycarbonate sheets are chosen for their clarity, impact resistance, and chemical stability.
Step 2. CNC Routing: To achieve precise shapes, CNC routers are used to cut the polycarbonate sheets. This technique ensures accurate measurements, critical for enclosures and shield screens that require exact specifications.
Step 3. Bending: Polycarbonate screens are often bent to form 90-degree angles using a line bender. This method allows for the creation of angled structures that fit specific setups. The attached images show the meticulous bending process, with measurements confirming an exact 90-degree angle.
Step 4. Assembly and Finishing: Once cut and bent, the screens are finished to remove any sharp edges or imperfections, ensuring a safe and polished final product.

Technical Specifications
- Material: Polycarbonate
- Thickness: Customisable
- Clarity: High optical clarity
- Impact Resistance: High
- Temperature Range: Suitable for a wide temperature range
- Bend Angle: 90 degrees (as demonstrated)
- Manufacturing Tools: CNC Router, Line Bender
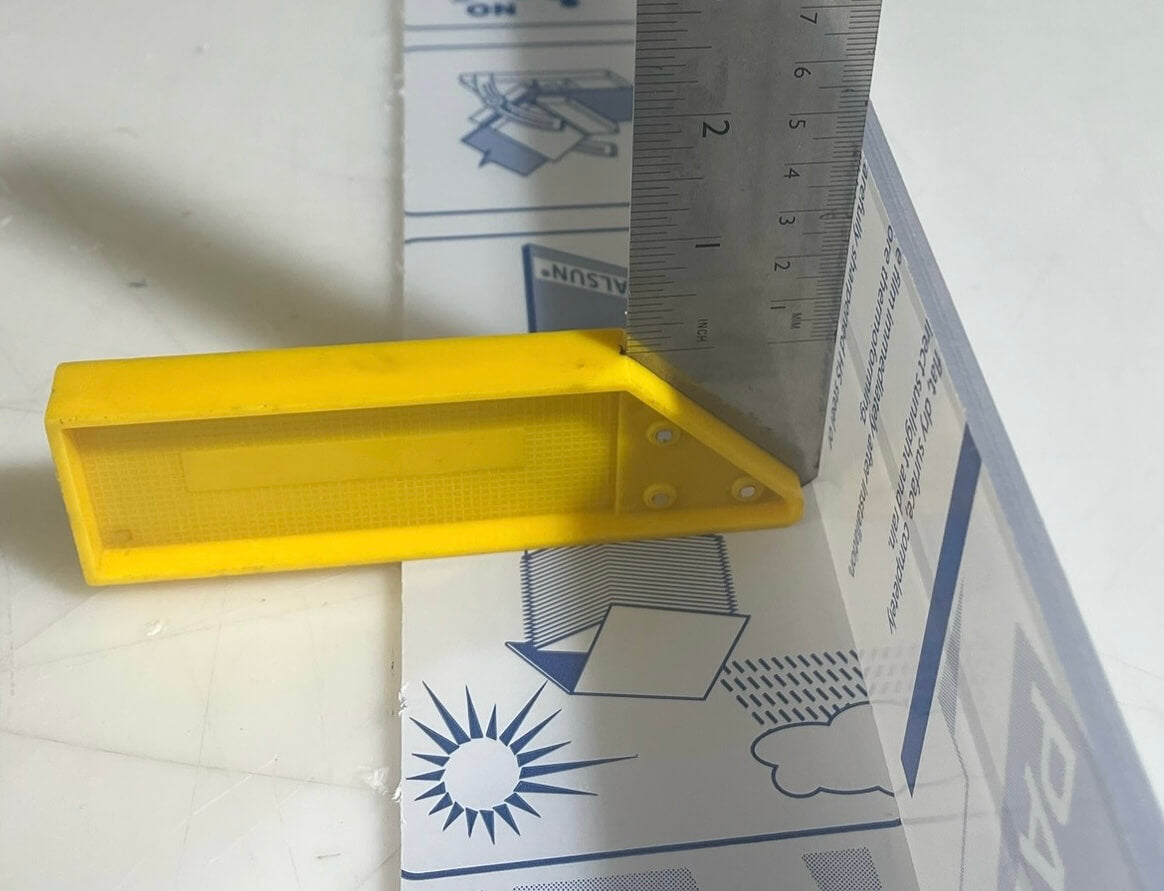
Final thoughts from WKH
Polycarbonate shield screens provide a safe, durable, and effective solution for the electrochemical sector.
The use of CNC routing and precise line bending ensures that these shields are accurately produced to fit specific applications.
With their high impact resistance, clarity, and chemical stability, polycarbonate shields are ideal for protecting both workers and processes in electrochemical environments.
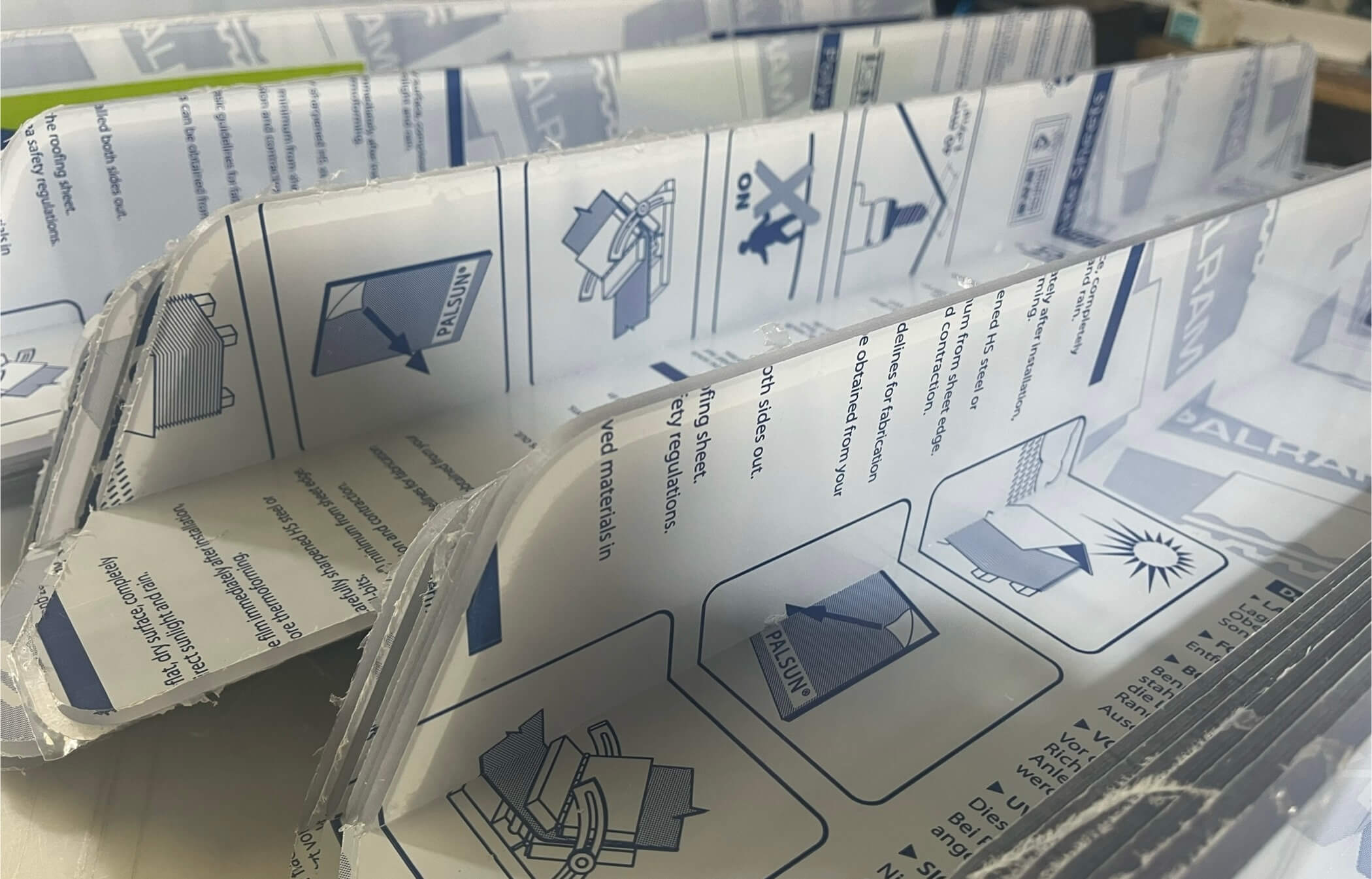
Book your next project
At WKH we offer a wide range of services tailored to the exact needs of our customers.
Require some plastic components or parts? At WKH we adapt to meet your exact requirement - simply call on 0113 239 1909, email us or request a quote.
Get Your Quote